Los componentes de sistemas neumáticos para aviones comerciales deben cumplir dos requisitos:
Componenetes del sistema neumático de potencia
El sistema neumático es un sistema cerrado. Los componentes básicos del sistema son: compresores, botellas de almacenamiento de aire de alta presión, válvula de descarga de presión, válvulas reductoras de presión, válvulas de alivio de presión, y válvulas de control de flujo y martinetes neumáticos.
Compresor
El compresor es una bomba de pistones, de dos o cuatro etapas según las necesidades de presión del sistema. Normalmente es impulsado por el motor a través de la caja de engranajes. Hay también en el mercado compresores eléctricos. Los compresores de cuatro etapas suministran aire a presión hasta 3.500 psi (246 kg/cm2, aproximadamente).
El tipo de compresor más usado tiene dos cilindros con sus correspondientes pistones. Está preparado para realizar cuatro fases de compresión por cada revolución de la manivela del pistón, gracias a que comprime el aire tanto en el movimiento de subida como de bajada del pistón. Cuando el aire se comprime en las dos fases del cilindro número 1 pasa al cilindro número 2. Los dos pistones, colocados en serie, permiten realizar las cuatro fases de compresión de los sistemas neumáticos de muy alta presión.
Entre fase y fase el aire se enfría en un intercambiador de calor. Esto permite disminuir el trabajo necesario para obtener la relación de compresión prevista.
Martinetes neumáticos
Al igual que los martinetes hidráulicos, los martinetes neumáticos tienen la función de transformar la energía presente en el aire comprimido en movimientos lineales o giratorios de distintos mecanismos.
A diferencia de los martinetes hidráulicos, los martinetes neumáticos están expuestos a movimientos repentinos muy enérgicos. Ello se debe a la compresibilidad del aire. Por consiguiente casi todos ellos disponen de mecanismos contra sacudidas o de rebote, que amortiguan los impulsos de presión que reciben los pistones cuando se comunican con la línea neumática de servicio.
Botellas de almacenamiento de aire a presión
Las botellas de aire actúan como acumuladores de aire comprimido. Su función es suministrar aire a presión al sistema. Los compresores son meramente órganos de restablecimiento de la presión de aire de las botellas. La capacidad de las botellas debe ser suficiente para todos los servicios neumáticos, incluidos los de emergencia, para los que se dedica normalmente una botella específica.
El material empleado en la fabricación de las botellas es acero de muy alta resistencia mecánica Las botellas se someten a inspecciones y pruebas hidrostáticas de presión cada intervalo de tiempo especificado.
Cabe decir que el sistema también cuenta con los correspondientes manómetros para el control de las botellas.
Válvulas
De descarga del compresor
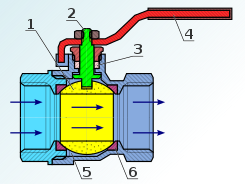
Esquema de una válvula de bola
Es la reguladora de presión del sistema. Tiene dos funciones principales:
- Controlar la presión máxima del sistema
- Permitir que el compresor funcione sin carga cuando el sistema no precisa de su funcionamiento.
Consiste en una válvula de bola que se abre cuando la presión a la salida de la segunda etapa de compresión sobrepasa un cierto valor. En este caso la válvula de bola alivia toda la presión de la tercera fase de compresión, funcionando el sistema solo con las dos primeras.
No obstante, las botellas de aire están a presión máxima, de manera que es posible cualquier servicio neumático. Si la presión en la línea cae por debajo de un cierto valor, la válvula de bola se cierra y de nuevo entran en funcionamiento los cuatro grupos de compresión.
Las válvulas de descarga mantienen la presión del sistema entre 2.900 y 3.300 psi. Si la presión del aire aumenta entra en acción la válvula antirretorno que "atrapa" el circuito, manteniendo la presión, mientras que la válvula de descarga dirige la salida del compresor a la atmósfera.
De lanzadera
Cumplen en los sistemas neumáticos de potencia la misma función que en los sistemas hidráulicos. Está situada entre el compresor y la línea principal. Cuando se conecta un carro neumático en la boca de servicio del sistema, la lanzadera se desplaza al otro extremo y permite cargar el sistema. En realidad esto sucede siempre que la fuente de presión de servicio en tierra es mayor que la del sistema, no solo cuando los motores del avión están parados.
Reductoras de presión
Las válvulas reductoras tienen la función de disminuir la presión de aire para los subsistemas que no requieren la alta presión de línea que mantienen las botellas. Las válvulas reductoras mantienen una presión diferencial aproximadamente constante, entre el subsistema y la atmósfera.
En realidad, la mayor parte de los componentes del sistema, incluido el tren de aterrizaje, puerta de pasajeros, etc, funcionan con presiones del orden de 1.000 psi (70 kg/cm2), esto es, valores inferiores a los máximos que puede suministrar el sistema.
De aislamiento o mantenedoras de presión
Como su nombre indica mantienen la presión en la línea, o en un segmento de ella. Es una válvula que manipula el técnico de mantenimiento para realizar servicios' en el sistema sin necesidad de tener que descargar todas las botellas de aire comprimido.
Purgador de agua
El purgador de agua tiene la función de eliminar el agua suspendida que puede estar presente en el aire que sale del compresor.
El aire entra en el purgador a la presión normal de salida del compresor, y es dirigido contra unos tabiques colectores de agua, donde se deposita. Cuando el sistema esta inactivo, y la presión del aire desciende por debajo de un determinado valor (digamos, 450 psi, equivalentes a 30 kg/cm2) se abre la válvula de drenaje y escurre el agua separada en el purgador. El aire de servicio entra finalmente filtrado en el sistema con malla de 10 μm, lo que da idea de su grado de limpieza.
Filtros
Se emplean para eliminar residuos y evitar que estos se depositen en los conductos y válvulas haciendo menos eficaz el sistema. Básicamente funcionan haciendo pasar aire a través de la malla filtrante o cartucho reteniendo las partículas. Los residuos se depositan en el fondo y si el filtro estuviese muy sucio, se abre una válvula de alivio que deja pasar el aire sin filtrar. El cartucho debe ser reemplazado con regularidad para evitar estas situaciones.
Deshumectador
El deshumectador elimina la humedad del aire comprimido. Se impide de esta forma la posible formación de hielo en las válvulas y tuberías del sistema.34
Sistema neumático de emergencia
Ll sistema neumático de potencia tiene su propio subsistema de emergencia, con botella de aire comprimido especifica para estos fines. Generalmente los aviones menos modernos hacen usu del sistema hidráulico normal, más otro neumático para emergencias, este último como respaldo del primero.
Por lo tanto se distinguen dos situaciones:
- En los aviones con sistema exclusivo neumático de potencia, el sistema de emergencia se alimenta del sistema principal, en tanto funcione, a través de una válvula antirretorno (dirección sistema principal-sistema de emergencia). Dentro del circuito de emergencia se incluyen el sistema de accionamiento de bajada de los flaps, tren de aterrizaje y la aplicación de frenos, entre otros.
- En funciones de sistema alternativo al hidráulico o hidráulicos principales
Tiene, no obstante la característica de disponer de una botella neumática de prioridad. Cuando la presión de las botellas de servicio desciende por debajo de un cierto valor, la válvula de lanzadera aísla el circuito de líneas prioritarias de tal manera que la botella neumática de prioridad alimenta solo a sistema esenciales del avión.
El sistema de emergencia de frenos neumático es controlado por el piloto, una vez que comprueba que el avión ha perdido la presión hidráulica. La carga de aire o de nitrógeno de alta presión se dirige a un depósito de transferencia, lleno de fluido hidráulico, que queda sometido a la presión del gas.
La presión neumática transferida al fluido hidráulico desplaza los pistones de los frenos, cuyos discos se someten ahora a presión hidráulica mantenida por la carga del gas a presión.
Nótese que no existe presión neumática en el paquete de freno. Es presión hidráulica procedente de la carga de gas a presión en la botella de emergencia.
La carga de gas permite la aplicación reiterada de los. frenos. Por ejemplo, en el antiguo Boeing 707 permite hasta cinco frenadas sucesivas.
Sistema de sangrado de aire
En relación con el sistema neumático del avión, se llama sangrado de aire a la operación de extraer aire caliente y a presión de uno o más de los compresores del motor. El fin es atender las necesidades de sistemas neumáticos utilitarios. Estos sistemas se dividen en dos categorías: principales y secundarios.
Los sistemas principales tienen funciones operacionales fundamentales. Son los siguientes:
- acondicionamiento de aire de cabina
- sistema de deshielo-antihielo
- en algunos aviones, sistema de cortina neumática de protección del parabrisas frente a la lluvia.
De forma colateral puede incluirse en esta clasificación la Unidad de Potencia Auxiliar (APU), dada su conexión íntima con el sistema.
Otros sistemas neumáticos tienen menor entidad desde el punto de vista operacional, como es el caso de los sistemas de agua potable y deshecho de desperdicios. Desde el punto de vista neumático tienen la característica común de simplicidad. A veces, la neumática se emplea únicamente para presurizar conducciones de fluidos. No obstante cada uno, en su esquema de servicio, es fundamental para los fines del avión comercial.
Los sistemas secundarios más relevantes son los siguientes:
- sistema de presurización de depósitos hidráulicos
- sistema de ventilación del compartimento de aviónica
- sistema de agua potable
- sistema de deshecho de desperdicios
CONCLUSIONES:
para mi es un tema escencial ya que gracias a la neumática, tenemos muchas de las máquinas y otras cosas que nos sirven para la vida diaria, ademas sin ellas no podriamos realizar muchas de las acciones en las cuales requerimos de la neumática y ademas el trabajo sería más arduo de no ser por esta.